BKT: il futuro dell’agricoltura – Intervista al product manager Denis Piccolo
Il mondo dell’agricoltura si prepara ad affrontare nuove sfide e a raggiungere nuovi traguardi tecnologici in processi, macchine e, naturalmente, anche pneumatici. Ne abbiamo parlato con Denis Piccolo, product manager per la divisione agricoltura del colosso indiano BKT, che ha la sua sede europea in Italia, a Seregno.
Come è cambiato il pneumatico agro nel corso degli anni?
Gli pneumatici per le macchine agricole nascono, nel passato, come bias (o convenzionali) e solo dopo è subentrata la versione radiale, che di fatto è il primo grande passo innovativo in questo settore. Dopo tanti anni di utilizzo dello pneumatico radiale, è sorta una nuova esigenza: montare dei prodotti in grado di minimizzare l’impatto al suolo e il compattamento del terreno, in modo da aumentare la produttività dei campi. Tanti anni fa si è, quindi, cominciato a studiare il modo di sviluppare degli pneumatici che fossero in grado di sostenere un carico maggiore, pur avendo una pressione inferiore. In altre parole, a parità di misura e quindi di volume d’aria, il mezzo può trasportare un carico più pesante.
La soluzione si è tradotta negli pneumatici IF (Improved Flexion) a bassa pressione, che caricano, a parità di pressione, il 20% in più rispetto a uno pneumatico standard e, successivamente, negli pneumatici VF (Very High Flexion) che sopportano un carico superiore del 40%. Il vantaggio di questa nuova tecnologia è davvero significativo, perché il compattamento del terreno è direttamente proporzionale alla pressione e quindi la produttività del terreno è significativamente maggiore.
Qual è la tendenza del mercato alla luce delle nuove tecnologie?
Il mercato oggi si divide tra radiale standard, da una parte, e radiale VF, dall’altra. Lo pneumatico bias sta progressivamente andando in disuso. Si salvano delle nicchie, come ad esempio le applicazioni forestali, dove si apprezza ancora lo pneumatico convenzionale, costruito con molte tele e con un fianco molto rigido e resistente. Oggi si cerca di impattare il meno possibile all’interno della foresta, percorrendo sempre gli stessi sentieri di lavoro, ma nel futuro è probabile che la tecnologia evolverà anche in questo settore. Sta, infatti, nascendo l’esigenza di impattare il meno possibile sul delicato sistema ecologico del sottobosco, soprattutto nei Paesi del nord Europa. Il sottocomitato tecnico degli pneumatici Agricoltura e Forestali dell’organizzazione ETRTO, (European Tire and Rim Technical Organization), di cui faccio parte, sta lavorando per definire i parametri tecnici da adottare per gli pneumatici dedicati al lavoro in foresta con un basso impatto sul suolo, quindi, in sostanza, di pneumatici VF specifici per il settore forestale.
Qual è l’offerta di BKT per l’uso forestale?
Abbiamo recentemente presentato i nuovi pneumatici forestali Forestland e Forestmax, che sono stati sviluppati per rispondere soprattutto alle esigenze degli operatori dei Paesi del nord Europa, come Finlandia, Svezia e Norvegia, ma molto richiesti anche in Germania.
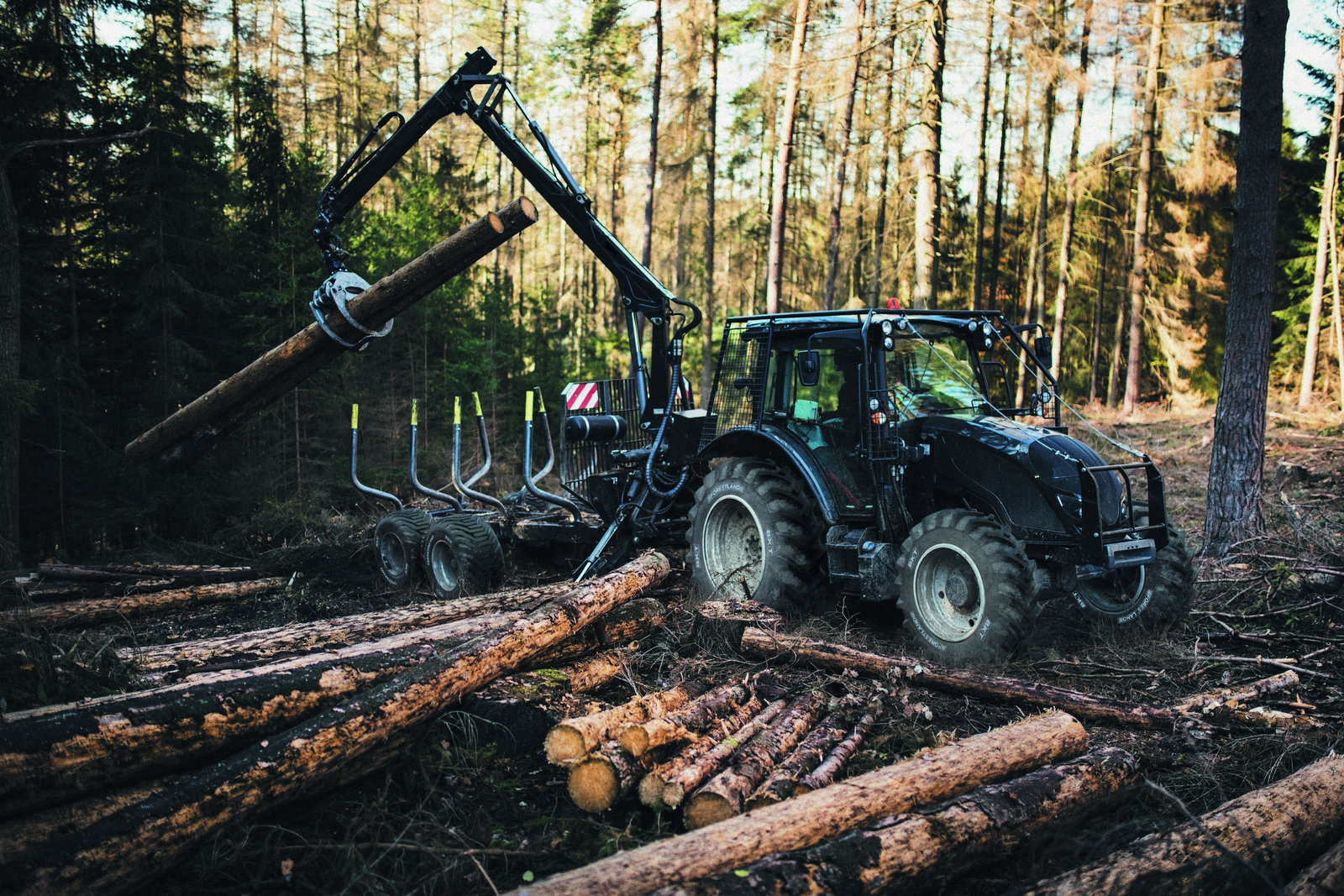
Il mercato cerca degli pneumatici forestali che possano essere, eventualmente, utilizzati anche in campo. Le specifiche delle due applicazioni sono, naturalmente, diverse, quasi opposte, e quindi l’una va a scapito dell’altra. Lo pneumatico convenzionale Forestland e quello radiale Forestmax lavorano benissimo in foresta e bene in campo.
Stiamo inoltre sviluppando dei nuovi modelli per forwarder che si spostano all’interno della foresta per le operazioni di taglio degli alberi. Oggi, gli pneumatici dedicati a questo segmento sono principalmente di tipo convenzionale, ma nel prossimo futuro qualcosa potrebbe cambiare in termini di riduzione della pressione e – di conseguenza – di compattazione del terreno. È un’idea per il futuro a cui si sta iniziando a lavorare sulla base dei calcoli e delle normative che sta sviluppando l’ETRTO.
Come si suddivide il mercato rispetto ai pneumatici VF, IF e radiali?
Gli pneumatici IF, che rappresentano una via di mezzo tra lo pneumatico standard e quello VF, stanno lasciando il campo ai più moderni VF, oppure ai radiali. Sempre più, sia i primi equipaggiamenti che l’utente finale preferiscono investire nella tecnologia VF, rispetto a quella IF, oppure rimanere sullo standard radiale.
Gli pneumatici VF sono nati, in origine, per aumentare la capacità di carico, abbassando le pressioni, ma al contempo la tecnologia VF è stata estesa anche agli pneumatici stretti, utilizzati per fare i trattamenti con gli atomizzatori nelle colture a filare. In questo caso la tecnologia VF non serve per diminuire l’impatto a terra, che viene evitato il più possibile passando sempre per lo stesso tracciato, ma per aumentare la capacità di carico degli sprayer con i tank che trasportano i liquidi. Questa esigenza è sentita soprattutto negli Stati Uniti e in Australia, dove sia le macchine che i campi sono enormi. Lo scopo dei VF è quindi duplice: da una parte, compattare meno il terreno utilizzando pneumatici molto larghi e, dall’altra, aumentare la capacità di carico per i mezzi con pneumatici stretti, che non sono interessati alla compattazione del terreno.
Negli ultimi anni sono nati anche gli pneumatici VF Flotation per i trailer agricoli, che anche loro lavorano in campo. L’intuizione era giusta e ha portato successivamente alla nascita degli pneumatici VF anche per i trailer.
Quali sono le ultime novità nell’offerta VF di BKT?
Abbiamo sviluppato lo pneumatico Agrimax V-Flecto, le cui prestazioni, già molto apprezzate dal mercato, sono state confermate dai test comparativi eseguiti dall’Istituto tedesco indipendente DLG. Le misure testate sono VF650/65 R42 e VF540/65 R30, che hanno ottenuto risultati eccellenti oltre le nostre più ottimistiche previsioni. Avere nero su bianco dei risultati, consultabili a questo report, che hanno superato tutte le nostre aspettative, è una grande soddisfazione. Agrimax V-Flecto è un prodotto incredibile. Il nostro obiettivo era verificare, rispetto alla concorrenza, il comportamento del nostro pneumatico a livello generale, ma, in particolare, riguardo alla compattazione, alla capacità trattiva e al consumo di carburante.
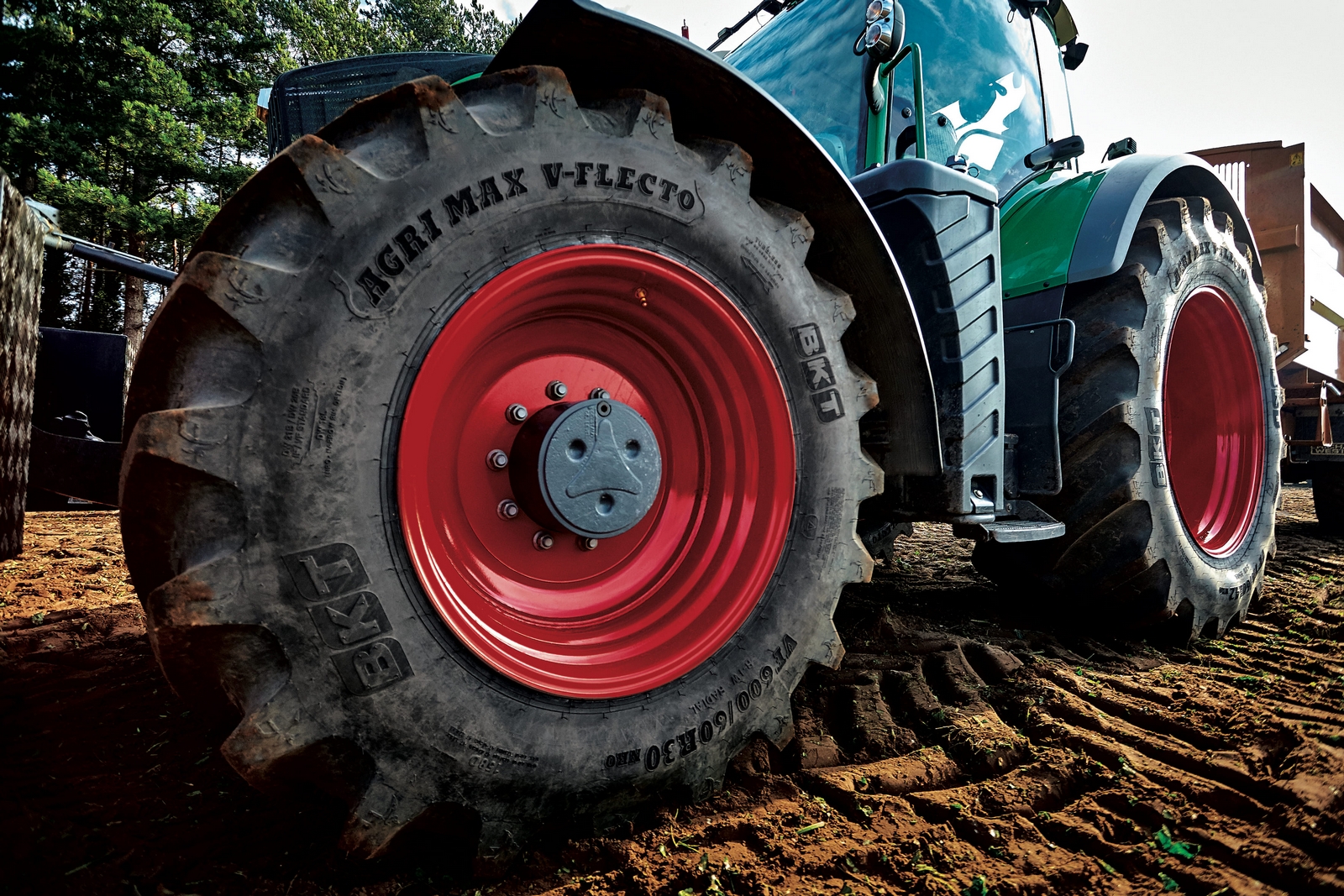
Misurare e confrontare il consumo di carburante è molto difficile, in quanto è legato a tantissimi fattori e variabili difficilmente ripetibili, come ad esempio la macchina, la temperatura del motore e della trasmissione, il terreno, ecc. Per questo, DLG ha sviluppato un sistema indoor con un banco di prova a rulli che consente di mettere a confronto gli pneumatici mantenendo le stesse condizioni. Ebbene, siamo risultati quasi sempre i migliori per ogni tipologia di test effettuato, mentre in un paio di prove siamo stati in linea con un concorrente primario. I risultati sono stati superiori alle nostre aspettative: nonostante fossimo convinti delle prestazioni del prodotto, considerando le informazioni provenienti dal mercato, non pensavamo di essere a questi livelli. Siamo risultati i migliori per compattazione e consumo di carburante e assolutamente in linea con i leader di mercato per la capacità trattiva.
Che futuro c’è per i cingoli nel settore agricolo?
Il cingolo è un mondo completamente a parte, un altro pianeta. Negli ultimi 25 anni la diffusione dei cingoli ha avuto un andamento sinusoidale, alternando momenti di picco e fasi di inutilizzo. Negli ultimi anni stanno riguadagnando terreno poiché utili per alcune applicazioni, come nel caso di terreni molto umidi, come le risaie, dove serve una buona trazione.
Ma il cingolo presenta vantaggi e svantaggi. Nei campi immensi con macchine estremamente potenti, come negli USA, possono essere vantaggiosi: maggiore capacità trattiva, minore consumo grazie all’inferiore slittamento rispetto allo pneumatico e inferiore compattamento dato da una maggiore impronta. Uno degli svantaggi principali riguarda, invece, il fatto che serve un raggio di curvatura molto ampio per effettuare le manovre di cambio di direzione. Insomma, la scelta del cingolo dipende tanto dal tipo di applicazione. In Europa, ad esempio, si sta diffondendo l’utilizzo degli pneumatici all’anteriore, che consentono di sterzare bene, e dei cingoli, sul posteriore, che garantiscono maggiore capacità trattiva.
Noi stiamo andando avanti a sviluppare i cingoli per l’agricoltura, soprattutto per le mietitrebbie, in minor misura per i trattori. Siamo ancora agli albori e dobbiamo fare esperienza, perché il cingolo presenta problematiche diverse rispetto allo pneumatico, che sono molto complesse. Per noi è una sfida, che abbiamo voluto cogliere. Vediamo come si evolverà nei prossimi anni. Al momento ci sono alcuni leader del settore con decenni di esperienza, ma se il mercato si svilupperà e se noi ci impegneremo come abbiamo fatto per gli pneumatici, nel giro di 5-6 anni saremo in grado di presentare una gamma di prodotti interessanti.
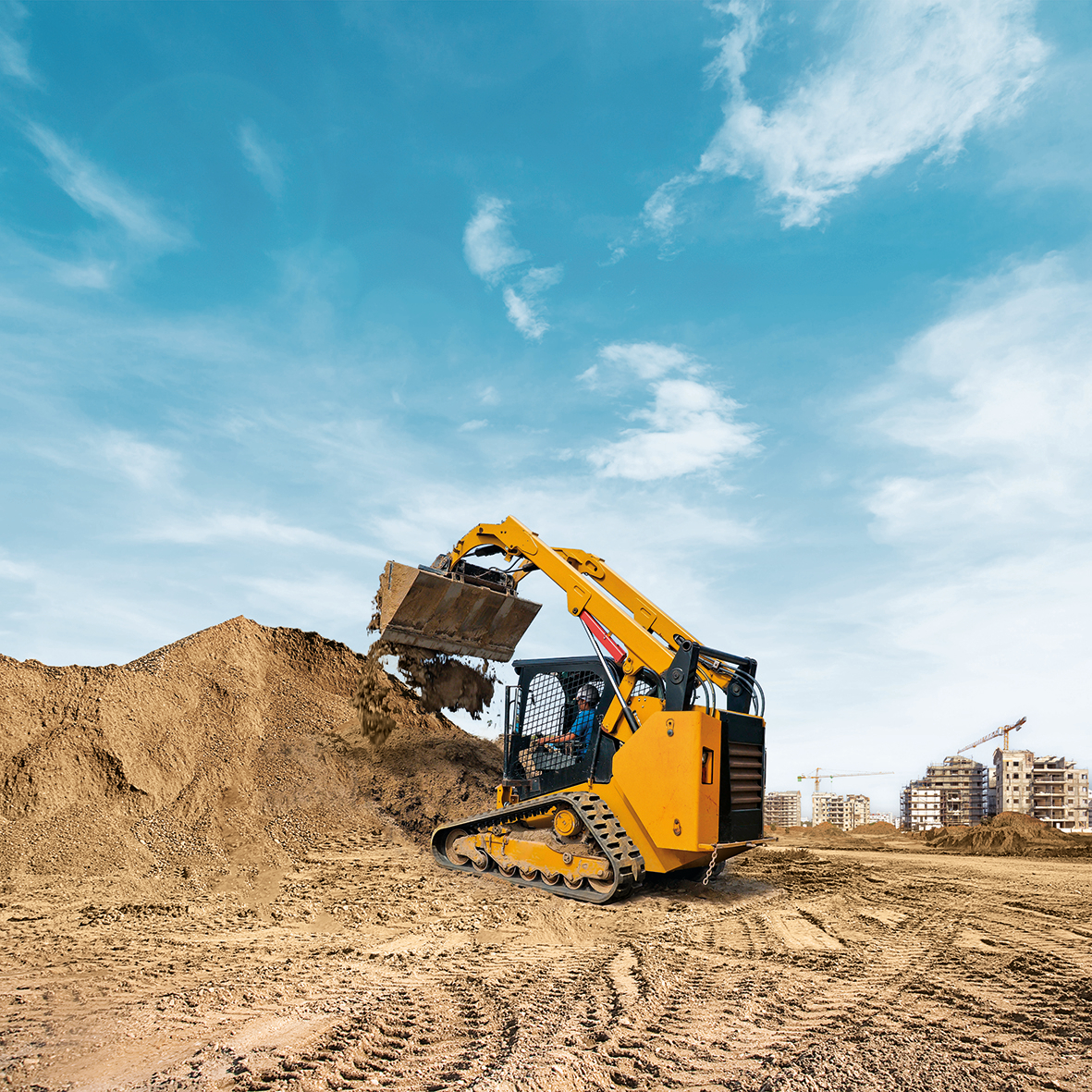
Quali sono le ultime novità BKT per i rimorchi?
PowerTrailer è il nostro ultimo nato, uno pneumatico radiale All-Steel per l’utilizzo sia su strada che in campo. Questo pneumatico nasce da un’esigenza di mercato che si propone di soddisfare le necessità di chi fa percorre tratti su strada, provocando un inevitabile stress elevato che si ripercuote sugli pneumatici a causa del carico e della velocità. I primi risultati sono molto incoraggianti e il mercato sta rispondendo con entusiasmo, anche perché il trattore viene utilizzato sempre di più come mezzo di trasporto.
In finzione di quello che chiede il mercato noi cerchiamo di sviluppare e proporre il prodotto più adatto. Oggi la gamma BKT è davvero ottimale e copre tutte le varie esigenze del mercato.
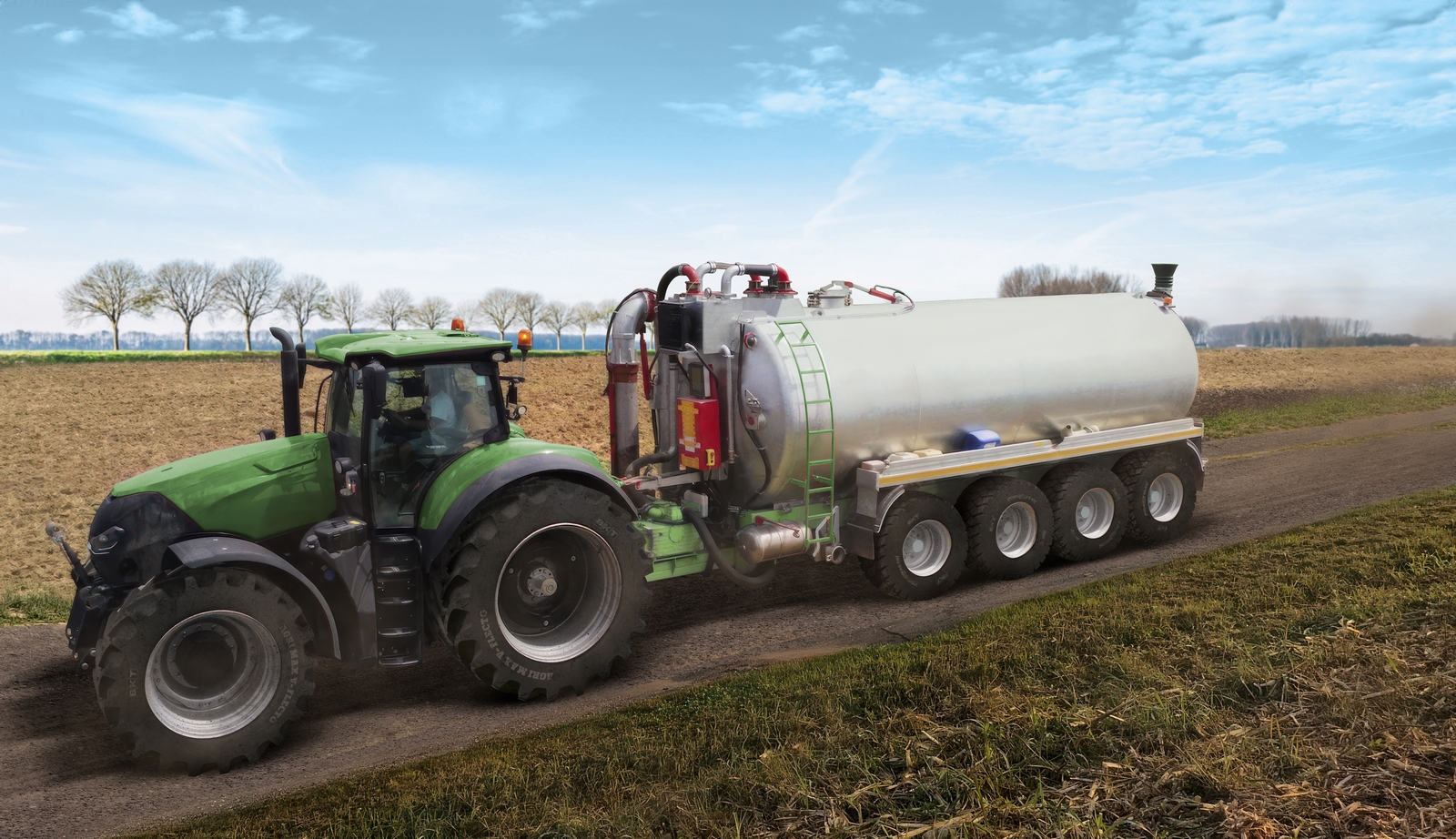
C’è un futuro per i motori elettrici nel mondo dell’agricoltura?
BKT ha iniziato a fare degli studi sulla rumorosità dovuta all’impatto dello pneumatico sull’asfalto. Con l’avvento dei motori elettrici, la rumorosità degli pneumatici che con il motore endotermico viene coperto, nasce l’esigenza di ridurre la rumorosità dello pneumatico non solo in cabina, ma anche per l’ambiente esterno, ossia per la cittadina che può essere infastidita dal rumore dell’impatto a terra degli pneumatici stessi. Il tema è molto complesso, per questo motivo è stato deciso di applicare una metodologia mutuata dall’automotive e dall’industria dell’elettrodomestico, che non è mai stata utilizzata per i trattori e gli pneumatici. In pratica, anziché utilizzare il classico decibel come unità di misura del livello di rumorosità, utilizziamo il son, un’unità di misura che definisce la qualità del suono. Esiste, infatti, una sorta di indice di gradimento del suono, che è stato realizzato da alcune università negli anni passati. Si tratta di una misura lineare e non esponenziale come il decibel.
L’obiettivo del nostro studio è capire cosa influisce di più sulla qualità del suono, dal punto di vista costruttivo dello pneumatico: pattern, costruzione carcassa, materiali utilizzati, ecc. Il risultato finale dipende però anche dal trattore, il cui suono va in risonanza con la cabina, in funzione delle caratteristiche costruttive dello stesso. Parliamo quindi di un tema molto complicato. Abbiamo comunque iniziato questa tipologia di studio, che punta a migliorare da una parte la sonorità e, al contempo, a ridurre la resistenza al rotolamento, studio già applicato allo pneumatico AgrimaxFactor, lanciato a inizio 2023. AgrimaxFactor si fregia infatti del logo E-Ready, che ne certifica il possibile utilizzo futuro sui trattori elettrici.
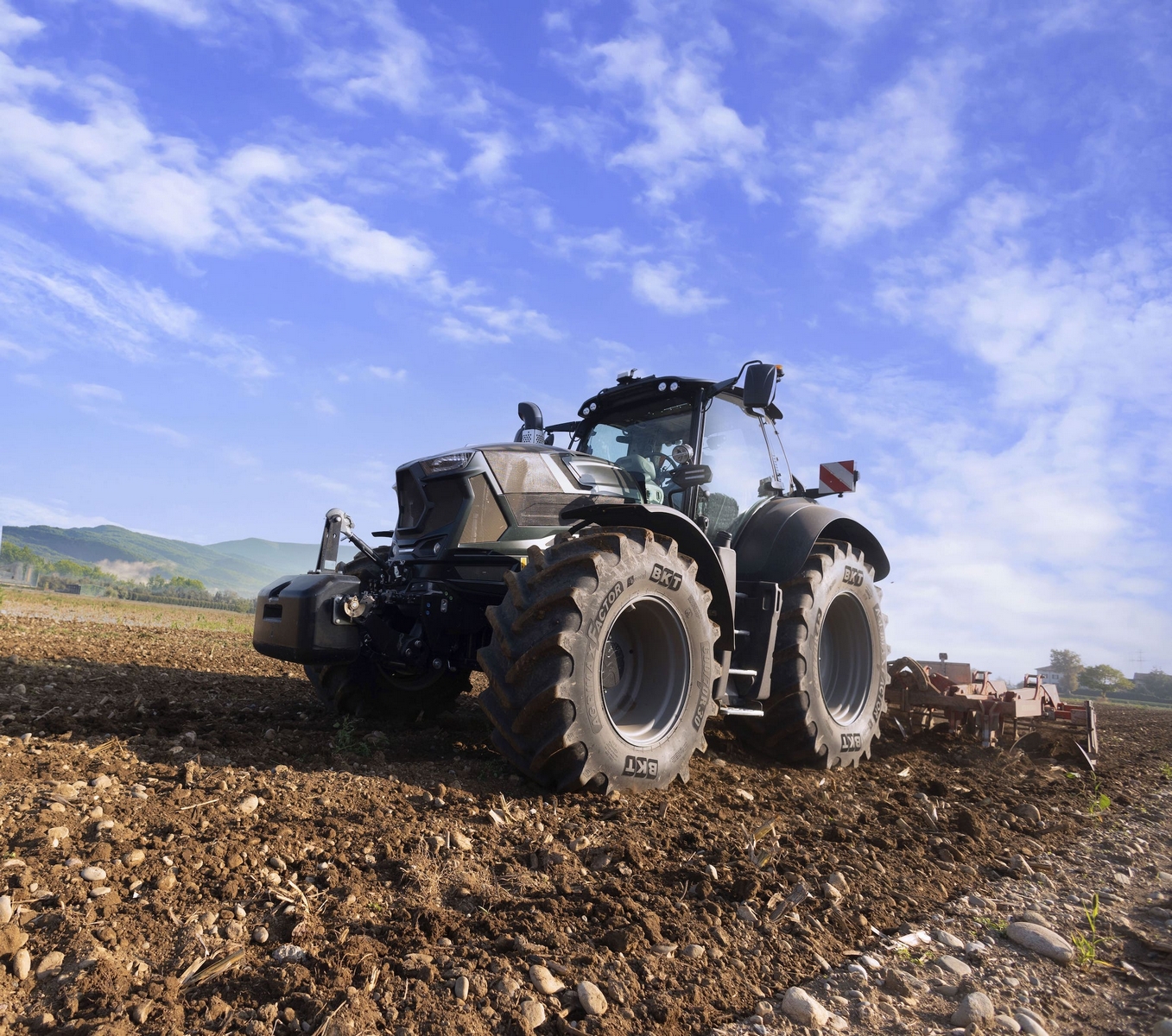
Disegno, mescole e materiali della carcassa sono cambiati per incontrare, in futuro, questa esigenza. È un primo passo, ma non so dire se e quando i motori elettrici entreranno nel settore agricolo. Per le macchine ad alta potenza non vi sono ancora le condizioni tecniche adeguate, mentre per i piccoli trattori da frutteto potrebbe rappresentare un’opportunità.
Di fatto è una novità a cui il mercato è sensibile, per cui abbiamo cominciato a pensarci, ma dobbiamo vedere quale sarà la tendenza e come gli utenti risponderanno in base a parametri come, ad esempio, l’autonomia e i tempi di ricarica. Per adesso è un punto di domanda, ma personalmente ritengo che la strada dell’alimentazione a idrogeno possa essere molto più interessante.
Quali sono le caratteristiche che distinguono il mercato italiano?
Lo possiamo dividere in due grandi categorie: il contoterzista e l’agricoltore più o meno grande. Il contoterzista ha soprattutto l’esigenza di usare un prodotto il più flessibile possibile, che si adatti a tutte le condizioni. Uno pneumatico VF può essere ideale sia per il campo, dove diminuisce l’impatto sul terreno, sia per spostarsi da un campo all’altro, senza dover modificare le pressioni. Chiaro che, se la strada da percorrere è tanta, non è possibile viaggiare a basse pressioni senza consumare moltissimo carburante e sottoponendo lo pneumatico ad un elevato stress. Quando però i campi sono vicini, lo pneumatico VF è perfetto.
È un tipo di target che si rivolge in maniera molto specifica al tipo di lavoro che fa e che, all’interno della nostra gamma, può trovare una risposta per ogni sua esigenza, grazie anche al supporto dato dai nostri esperti, a partire dai venditori dei nostri distributori.
Il piccolo agricoltore, invece, molto probabilmente non compra il VF, che ha un costo maggiore, ma preferisce lo pneumatico standard, sufficiente per le sue esigenze.
Il nostro è un mercato molto variegato, come sempre in Italia: ci sono tantissime piccole imprese, perché non abbiamo la capacità di fare gruppo. È la nostra forza e il nostro difetto ed è così anche nel mondo dell’agricoltura.
Per quanto riguarda i cingoli, il mercato è attivo in particolare nel centro Italia, ad esempio nelle Marche, una regione caratterizzata da colline e in cui, in alcuni casi, si può ancora trovare chi esegue l’aratura con trattori con cingoli in acciaio. Oppure nelle zone delle risaie. Il cingolo, più che nell’agricoltura, è molto usato nel mondo industriale, su mini-escavatori o pale. Un settore, però, particolarmente attento al prezzo, al contrario di quello agricolo che è invece un mercato molto tecnico e, dunque, più focalizzato sulla qualità del cingolo.
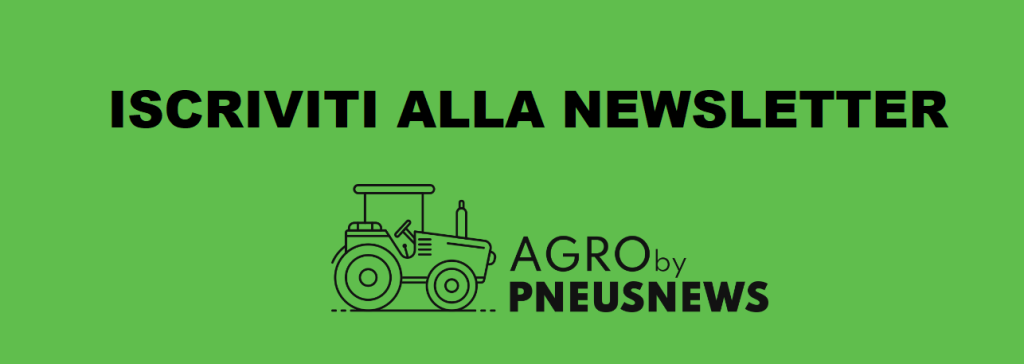